As interest in 3D printing for construction (3DPC) grows, it comes with a precondition. Concrete is used; a material associated with high CO2 and GHG emissions.
With so much recent focus on the development of low-carbon and even zero-carbon concrete, the blending of these developments could add to 3DPC’s many advantages that include reduced material waste, speedier in-situ construction, improved work safety and potentially lower costs.
It’s beginning to happen. In late December 2024, scientists at Nanyang Technological University, Singapore (NTU Singapore) announced the development a 3D concrete printing method that captures carbon.
“The newly developed 3D concrete printing process involves injecting steam and CO2, captured as the byproducts of industrial processes, into the mixing concrete,” the university said in a .
The pumping of CO2 and steam into the concrete mix as the structure is printed allows the CO2 to react with the components in the concrete, turning into a solid form that sequesters and stores the carbon.
Lab researchers determined the new process absorbed and trapped 38 per cent more carbon than traditional 3D printed concrete methods.
What is also exciting is that this new process does more than just reduce the carbon footprint of the concrete used.
“Results have showed that the CO2 and steam injection method improved the mechanical properties of the concrete, offering increased strength compared to conventional 3D printed concrete,” the university says.
In terms of measured results, compression strength was improved by 36.8 per cent with up to 45.3 per cent higher bending strength.
Lab testing also indicated a 50 per cent improvement in printability, meaning the mixture can be shaped and printed more efficiently.
Co-author Dr. Daniel Tay, research fellow from NTU School of MAE, said, “Our proposed system shows how capturing carbon dioxide and using it in 3D concrete printing could lead to stronger, more eco-friendly buildings, advancing construction technology.”
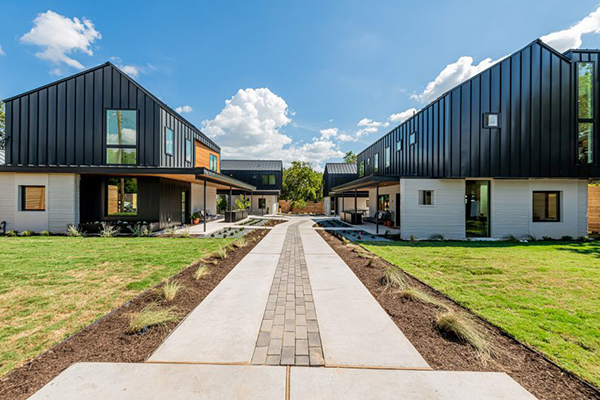
A U.S. patent application has been filed jointly by NTU and study collaborators. However, the researchers are not resting there. They hope to further optimize the process by using waste gases instead of pure carbon dioxide.
There’s more 3D printing research and announcements coming from other parts of the world.
Researchers at the University of Virginia (UVA), in collaboration with researchers at Virginia Transportation Research Council, have combined graphene with limestone and calcined clay cement (LC2), to develop a more sustainable, printable cementitious composite. They their new material offers enhanced strength and durability while significantly reducing carbon emissions.
“The addition of graphene to LC2 cement offers a unique opportunity to lower carbon emissions while maintaining the strength and flexibility required for 3D printed construction,” said Osman Ozbulut, a professor at UVA’s department of civil and environmental engineering.
According to the researchers, a life cycle assessment revealed this graphene-enhanced LC2 concrete could reduce greenhouse gas emissions by approximately 31 per cent compared to traditional printable concrete mixtures.
conducted in Ozbulut’s resilient and advanced infrastructure lab at UVA witnessed encouraging results when exploring the use of the emerging plant-based material Cellulose Nanofibrils in 3D concrete printing.
Cellulose Nanofibrils are made from wood pulp, the university explained.
“This creates a material that’s renewable and low impact. Like other plant-fibre derivatives, CNF, as the material is known in industry, shows strong potential as an additive to improve the rheology — the scientific term for flow properties — and mechanical strength of these composites.”
Analysis of tests using varying amounts of CNF additive found adding at least 0.3 per cent CNF significantly improved flow performance. Microscopic analysis of the hardened samples revealed better material bonding and structural integrity.
Printing in 3D with concrete means dealing with contradictory objectives, Ozbulut explained, adding there is a lot of trial and error when formulating the mixtures.
“The mixture has to flow well for smooth fabrication, but harden into a stable material with critical properties, such as good mechanical strength, interlayer bonding and low thermal conductivity.”
John Bleasby is a freelance writer. Send comments and Inside Innovation column ideas to editor@dailycommercialnews.com.
Recent Comments
comments for this post are closed